Machine Capabilities vs. Functional Requirements: Finding the Balance in Precision Manufacturing
- DMAC Machining
- 14 minutes ago
- 4 min read
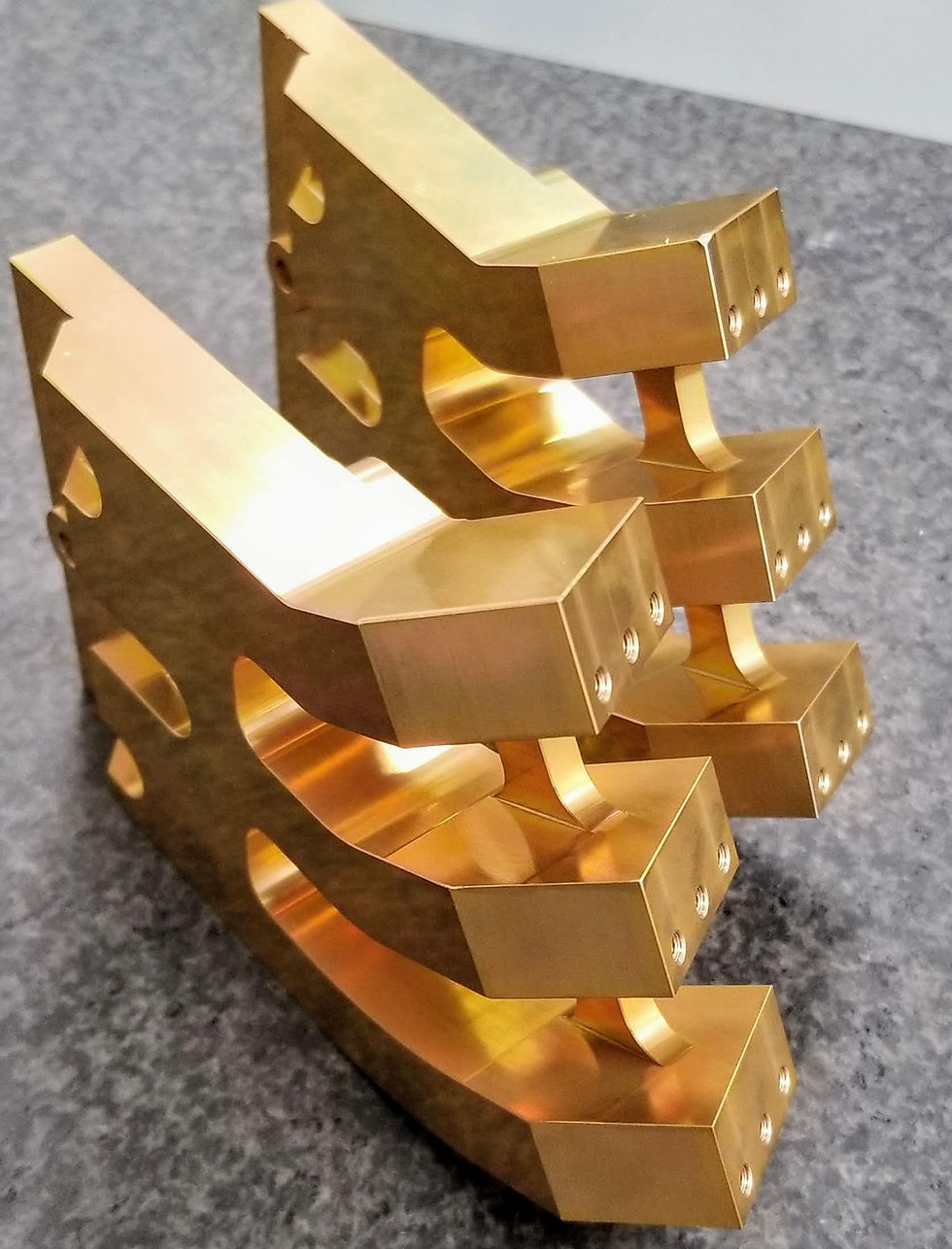
At DMAC Machining, precision is at the core of everything we do. As a machine shop specializing in advanced 3 and 5-axis machining, we work with client-provided designs and must find ways to meet the specified tolerances within the capabilities of our equipment. Often, we encounter drawings with tolerances that are tighter than necessary for the part’s function, adding complexity without providing tangible benefits.
Understanding the distinction between a machine’s capabilities and the functional requirements of the parts we manufacture is crucial to optimizing production, reducing costs, and ensuring quality.
Understanding Machine Capabilities for Functional Efficiency
Modern CNC machines achieve exceptional accuracy, often within a few microns, ensuring precision suitable for complex manufacturing. However, every machine has inherent limitations, and certain extreme tolerances may require specialized processes beyond standard machining operations. When designs include overly tight tolerances, additional steps such as fine-tuning setups, secondary operations, or post-processing may be required to achieve the specified precision.
Functional Requirements: What’s Really Needed?
Functional requirements refer to the actual specifications in a part’s drawing that determine how it will perform in its final application. These requirements often have little to do with the maximum possible precision the machine can achieve. Instead, they focus on the part's functionality—such as its fit in an assembly or its interaction with other components.
For example, a part might be required to fit into an assembly, but the specified tolerance for that fit could be more precise than necessary for proper function. Yet, we frequently see callouts that exceed practical machining limits or require additional processing steps to achieve.
The Impact of Overly Tight Tolerances
When parts are specified with tolerances much tighter than functionally necessary, several issues arise:
Increased Cost and Time: Extremely tight tolerances often require additional machining steps, specialized tooling, or multiple inspection stages, all of which add cost and lead time to the project.
Potential for Quality Challenges: Pushing machines to their absolute limits increases the scrap rates, all of which impact efficiency.
Unnecessary Complexity: When tolerances are tighter than required for functionality, parts may need extra finishing processes, higher rejection rates may occur, and the overall efficiency of production is reduced.
True Position and Threaded Holes in precision machining
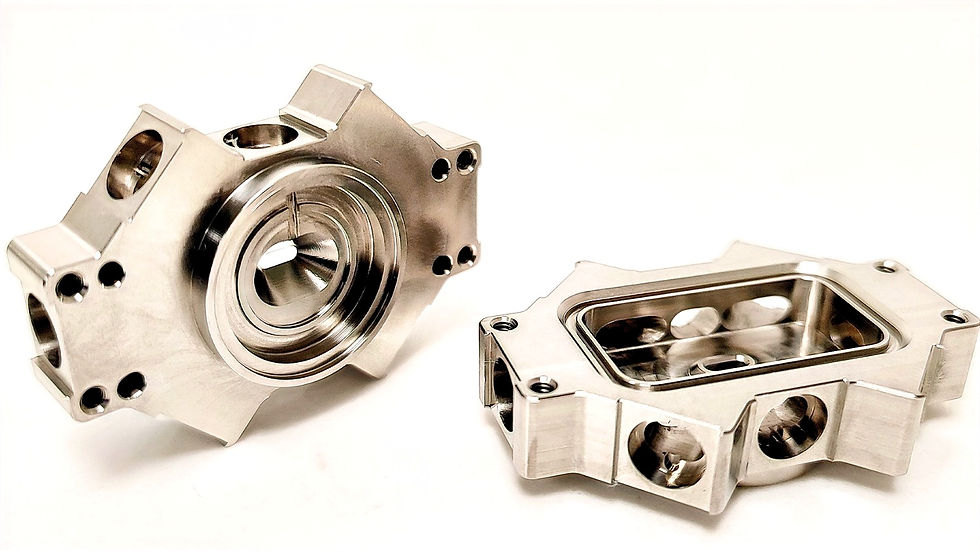
True Position is a crucial concept that dictates the allowed variation of the location of features, such as holes, from their theoretical positions. True Position ensures that features like holes, slots, or other critical geometries are positioned accurately relative to each other and the part’s reference point.
True Position for Holes
When a hole location is specified with a True Position tolerance, it indicates that the hole's center location must fall within a specific circular tolerance zone of the “true” theoretical perfect. In some cases, this tolerance zone can necessarily grow or shrink based on how close to perfect size the actual hole is. Achieving this tolerance ensures that holes are properly aligned for their intended application, such as for a dowel pin, which is essential for proper assembly.
Threaded Holes and True Position
The “true position” of a threaded feature is defined by the location of the pitch diameter of the threads. Standard measurement techniques do not allow the direct location measurement of the pitch diameter as it cannot be accessed directly. While it is possible to insert a Threaded Hole Location Gage into threaded holes to approximate their position this introduces variables larger than the small tolerance zone in which they are often specified.
These location gages thread into the hole and expand to “center within the threads” then have a positive “male” pin on the same center that can then be accessed by measuring instruments. The expansion in the threaded hole introduces variables that cannot be adequately accounted for. Additionally, these Threaded Hole Location Gages are quite expensive, in some cases hundreds of dollars each. When there are multiple threaded holes with True Position locations specified these gages must be moved multiple times from hole to hole. Manipulating these gages, and the part, once again introduces variables to the measurements.
The difficulty in measuring the “true position” of a threaded hole is why it is not recommended to rely on said holes as a location feature for the mating parts. Quite often we will see threaded holes specified with True Position Location tolerances of 0.025 mm (0.001”), well beyond the practical precision of the measurements that can be made, even with best practices and equipment. Not to mention, the industry standard for fastener size tolerances is often many times larger than the requested location tolerances of the threaded holes.
Best practices when a mating component needs to be located precisely would be to add locating dowel holes and dowels that can be verified to the required positional accuracy and leave the threaded holes and fasteners to just hold the parts together negating the need for tight tolerances on the location of the threaded holes.
How We Meet Tolerances Within Machine Capabilities
At DMAC Machining, we do not alter tolerances provided by our clients. Instead, we use our expertise in CNC machining to find the best approach to meet even the most demanding specifications within the capabilities of our machines. Here’s how we navigate these challenges:
Optimized Machining Strategies: We adjust tool paths, speeds, feeds, and work holding methods to maximize precision while maintaining efficiency.
Advanced Inspection Processes: For parts with extremely tight tolerances, we implement rigorous inspection techniques, including CMM verification, certified gages, and in-process probing, to ensure compliance.
Clear Communication with Clients: When we identify a design with tolerances that push the limits of machining or verification, we provide feedback on manufacturability and potential production challenges. While we never modify tolerances or specifications, we work closely with clients to ensure expectations align with achievable results.
Specialized Finishing Processes: In cases where machining alone may not achieve the desired precision, we use secondary processes such as grinding, honing, or lapping to meet the required tolerances.
Precision Doesn’t Always Equal Performance
At DMAC Machining, we recognize that the highest possible precision doesn’t always translate into better performance or more functional parts. Our role as a machine shop is to meet the tolerances specified by our clients while optimizing our processes to ensure cost-effectiveness and quality.
By working within machine limitations, leveraging advanced machining strategies, and applying best practices for features like threaded holes, we deliver high-quality parts while minimizing unnecessary complexity and cost. Precision machining is an art, and our expertise lies in knowing how to achieve the required tolerances efficiently and effectively.
Comments